Scrap Magnet Repair - ReManufacturing
Lifting Magnet Repair - What Is Reman®?
Winkle's ReMan program helps you reclaim value or extend the service life of damaged and out-of-service lifting magnets.
Comprehensive inspection, analysis and reporting processes all help take the guesswork out of your rebuild.
What can you expect?
ReMan incorporates a multitude of OEM specifications and strict rebuild guidelines that provide complete support through:
- Multi-Point Inspections
- Failure Analysis
- Upgrade Options
- Detailed Quotations
- Historical Data Tracking
For full details about the ReMan process, take a look at the full PDF by clicking here.
Steps we take for lifting magnet repair:
Steps we take for lifting magnet repair:
Step 1: Our comprehensive repair process begins with a thorough mechanical and electrical evaluation. Each magnet is assigned a unique job number, initiating a "Magnet Service Report."
Step 2: If the magnet passes initial electrical inspection, any mechanical issues are noted on the inspection report and sent to Customer Service for quotation. If the magnet fails incoming electrical tests, further evaluation and processes are used to determine the cause of the failure. If the secondary evaluation and processes do not recover the magnet’s electrical values, we will request permission to open the magnet for internal inspection.
Step 3: The magnet case undergoes careful disassembly. The components are examined, identifying those requiring reconditioning or replacement.
Step 4: Flat copper or aluminum conductor is unwound and is separated from the Nomex insulation undergoing thorough cleaning and inspection. All irregularities or damaged areas are noted as the conductor is spooled and set aside in order to re-use as much of the salvageable material as possible. Wire conductor, however, is typically not salvageable and is considered a total loss.
Step 5: At this stage, a detailed quotation is prepared and sent to the customer for approval.
Step 6: Following customer approval, mechanical parts are sandblasted, cleaned, repaired, or replaced depending on the work quoted.
Step 7: Our engineering team creates any necessary drawings for the production department, coupled with a detailed bill of material for the storeroom.
Step 8: Winkle magnet components are scrutinized against OEM drawings; other manufacturer’s magnets are compared to our extensive database for component tolerances.
Step 9: Coils are precisely wound turn by turn, incorporating Nomex insulation between each turn. The correct replacement conductor is employed as necessary, as improper conductor application can lead to poor performance or premature failure.
Step 10: Once the coil is properly insulated and installed in the case, the bottom plate is inserted and pressed into place before tack welding. Semi-automatic welding with stainless steel weld permanently seals the magnet, ensuring its integrity.
Step 11: The magnet if filled with a specially formulated insulating potting compound, baked at over 350º F to cure the potting compound.
Step 12: In the final stage, all magnets are placed on Winkle’s proprietary test bed where they are evaluated for both lift and electrical performance.
Step 13: Before shipment, the magnet is painted, and chains and pins are attached. The completed magnet is then sent to our Quality Control department for final evaluation prior to preparation for shipment.
Step 14: Winkle Industries delivers the highest quality new or remanufactured scrap magnet directly to your facility.
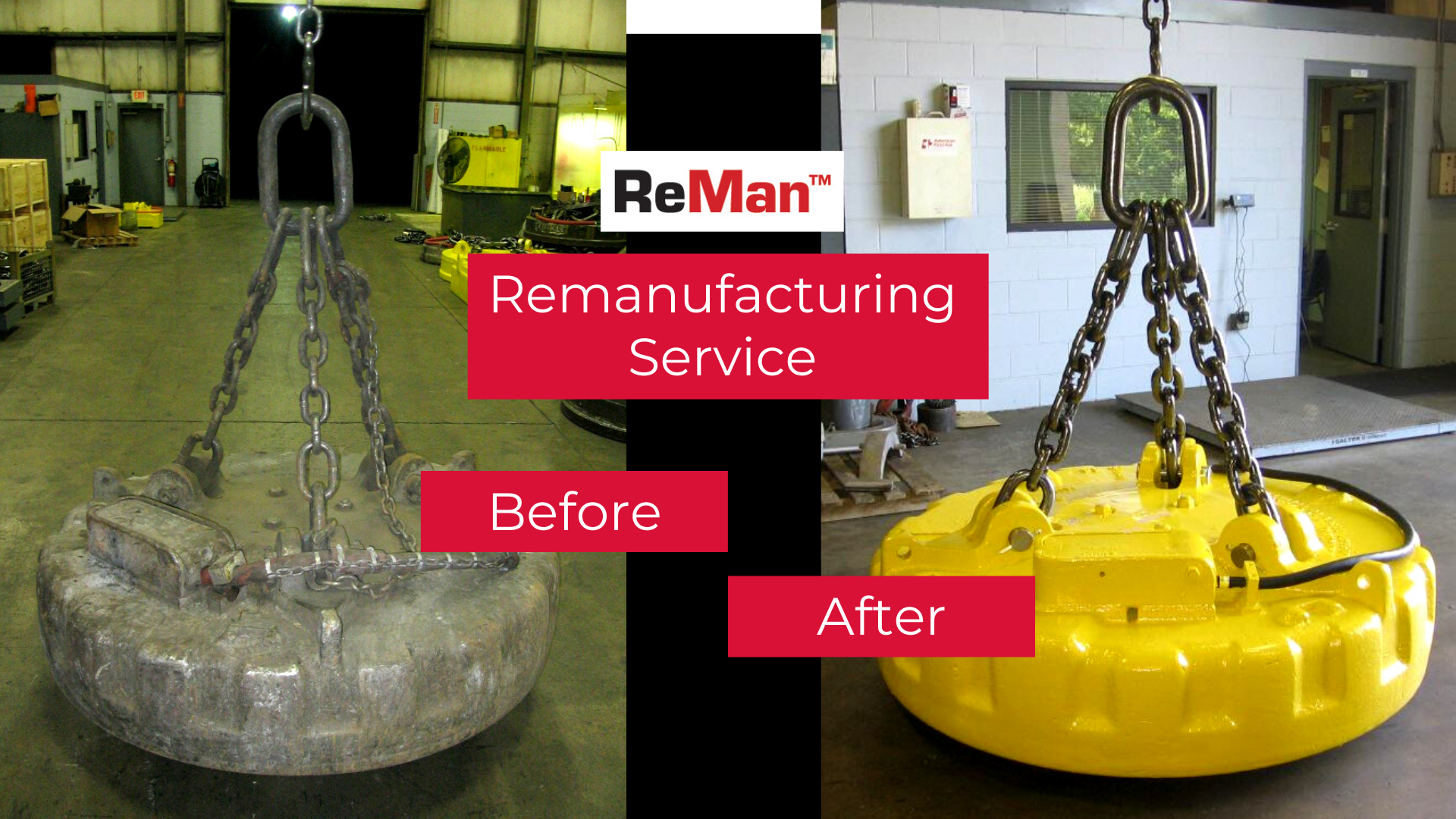